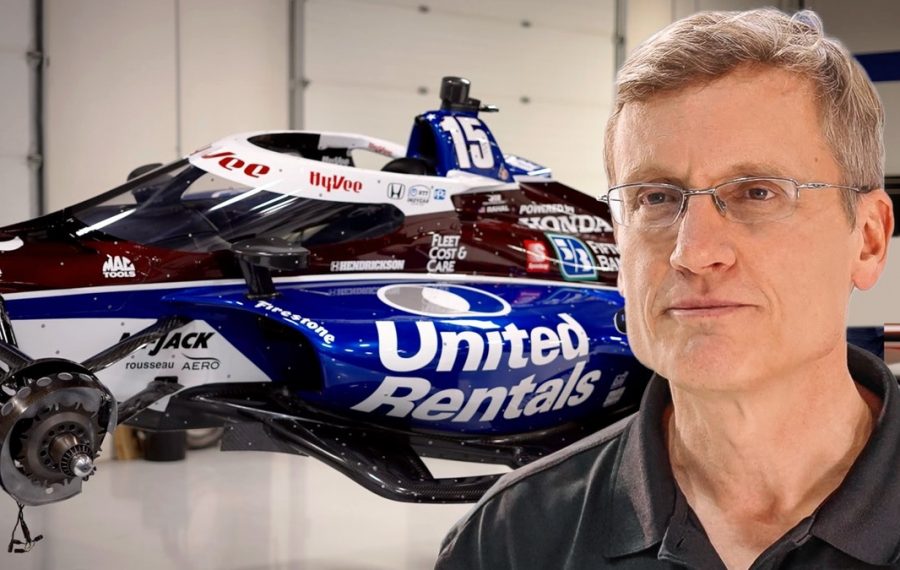
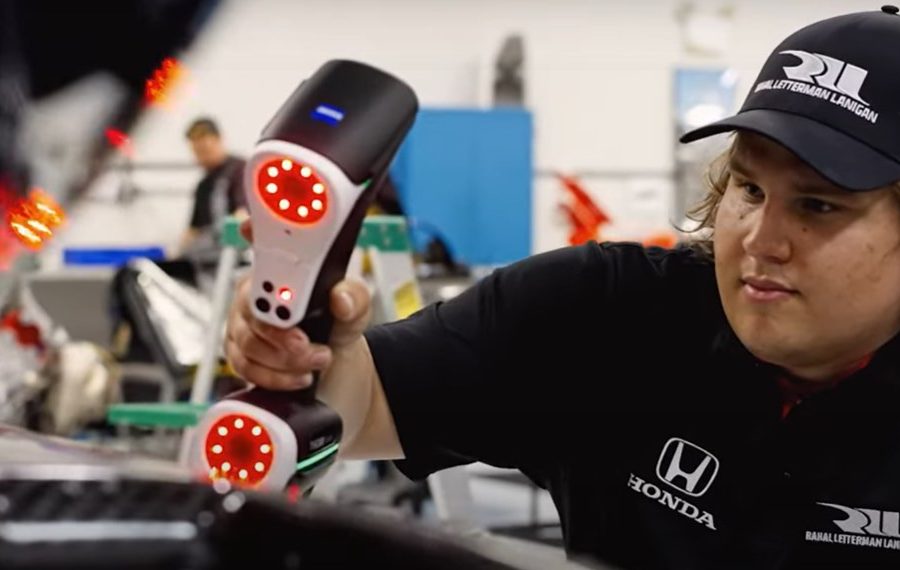
In IndyCar racing, after the race is before the race. What does that mean to you and your team?
Grant: Depending on the year, the IndyCar race schedule comprises some 17 races that are condensed into six to seven months. During that time, we have roughly two days per week to turn our cars over from race to race in between travelling. First, we completely disassemble them and break them up into front-end and rear-end mechanics. Then every part is looked over and checked for wear: cracks and imperfections.
Ricardo: After all, today’s wear mark is tomorrow’s failure. We look for anything that looks a little bit off.
Grant: When you reach speeds of around 240mph (385km/h), every imperfection becomes a safety issue. So, every little detail matters. If you make any mistake whatsoever, that’s the difference between a win and a loss.
Ricardo: Our cars are pretty mature. We’ve been running the same mechanical package since 2012. So, there’s a routine maintenance schedule. We’ve honed in on it over and over again, and we know exactly how long something will last before you have to rebuild it.
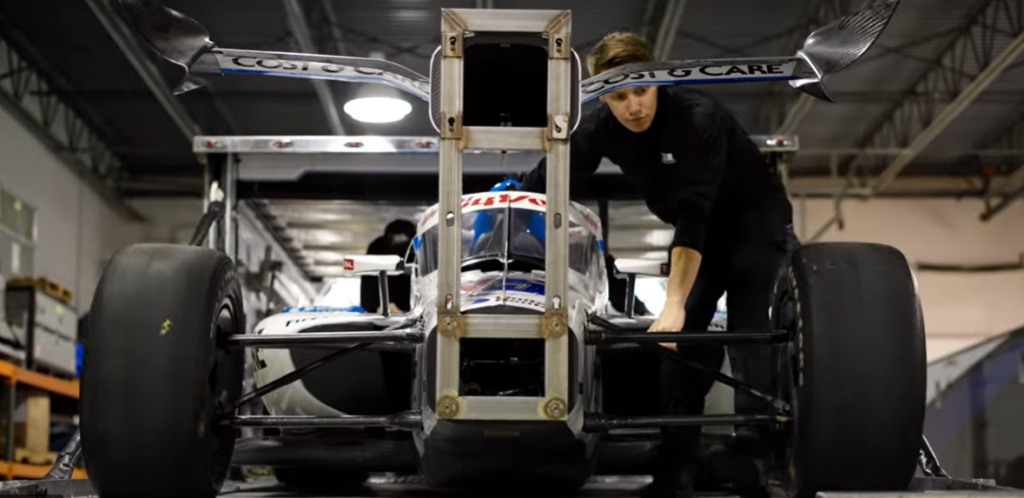
But IndyCar is a spec series: All the drivers race the same car model. How much room for adjustments do you have to improve your aerodynamics?
Grant: True, in the IndyCar series, everyone uses the same Dallara chassis. Every team then fits its cars with “aero kits”, such as front and rear wings or engine covers. Still, every part you get is from one or two manufacturers only – and since we’re talking about carbon molded pieces, they’re never exactly the same. After all, molds deteriorate over time, resulting in slightly different parts. It’s these small differences that might just make a big difference on the race track.
Ricardo: The mechanical stuff of our cars is very mature. We’ve got the easy stuff out of the way: how to get rid of the drag in the uprights and how to maximize our gearboxes. Now, it’s about getting down to the tiniest details. The bodywork is a big part of that: We want to maximize the airflow, so we have to look at how the air comes off the bodywork.
How do you do that?
Ricardo: As the years go by with the same car, you have to find new ways to keep making it better. I mean, those imperfections we’re looking for in between races you can’t even see with the naked eye. So, we’ve recently started using ZEISS scanners to for IndyCar 3D scanning. This way, we know exactly where they are in actual “tech space” compared to the design parameters and compared to each other.
Grant: First, we do a wind tunnel test and determine which one of our cars performs best. Then we return to the workshop and 3D scan the cars. After that, we compare the 3D scan data and the wind tunnel data of each car. Which small areas on the cars are different? What is the performance loss or gain due to those differences? We try to determine why this car is better than the other one – and aim to replicate the best car. It’s a huge endeavour, and 3D scanning our race cars makes it possible.
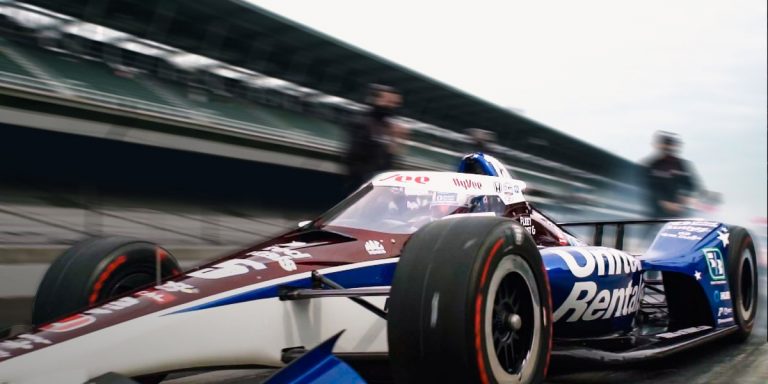
How many seconds do you get to shave off your races from using 3D scanning technology at the workshop?
Grant: In a spec series, such as IndyCar, you will never be able to find that one thing that makes your car a second faster. It’s more like 200 things that make you a quarter of a second faster – probably less. Again, every little detail makes a big impact.
Ricardo: The difference between first to 33rd position on the Speedway starting-grid has been condensed year after year after year. We need every tenth of a mile per hour. Every hundredth of a mile per hour even! You need a really defined instrument that gives you infinite detail. The 3D scanning of car parts fits that bill.
Has all your hard work paid off?
Ricardo: The IndyCar team at Rahal Letterman Lanigan Racing has had two Indy500 victories, the last one in 2020. We had great starting positions. All three cars were extremely strong. It was a great race, we had a great strategy, it was great driving by the drivers. Everything went according to plan. It has to go that way to win the 500. It has to go that way to win any race.